In addition to its composite aircraft, Overair will support infrastructure, aircraft operations and training to ensure a comprehensive and sustainable AAM ecosystem.
This initial project under the Space Act Agreement is focused on studying and developing high-performance battery cells, as well as performing safety testing, to achieve purpose-built solutions for electric aircraft. Facade Sandwich Panels
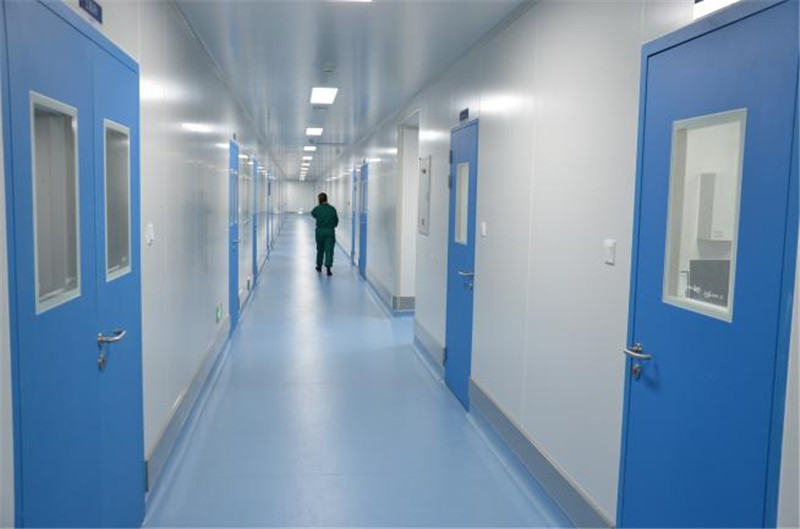
AeroZero TPS, applicable for metals and composites, will protect critical battery housing and parts in the Lilium Jet eVTOL aircraft from burn through and risk of thermal runaway.
V-tail, five-passenger aircraft builds on the vison of the S-A1, designed with a priority on safety and a focus on sustainability.
Agreement with green hydrogen producer extended for 2024, investment will support ongoing global capacity expansions including CFRP cylinder production.
Multifunctional four-axis winding system offering fiber flexibility will underpin the NCC’s work in testing and manufacturing pressure vessels leading to commercial production.
The new alliance will broaden National Composites’ capabilities in SMC and BMC and tooling, while providing customers with comprehensive solutions, from initial design to final delivery.
A new ASTM-standardized test method established in 2022 assesses the compression-loaded damage tolerance of sandwich composites.
Composites automation specialist increases access to next-gen technologies, including novel AFP systems and unique 3D parts using adaptive molds.
Combined LSAM and five-axis CNC milling capabilities will optimize D-Composites’ production services, flexibility and cut time and cost for composite tooling manufacture.
Evaluation of CFRTP m-pipe through Element’s U.K. facility aims to qualify the system for new operating environments.
Innovative prepreg tooling is highly drapable, capable of forming complex carbon fiber tooling shapes, in addition to reducing through thickness porosity and only requiring one debulk during layup.
Available as filament and granules for extrusion, new wood composite matches properties yet is compostable, eliminates microplastics and reduces carbon footprint.
A recent study conducted on vacuum-infused thermoplastic fiber-metal laminates has highlighted the performance benefits behind using TFP’s nonwovens for consistent, uniform bondlines and interfacial bonding.
To incorporate more environmentally conscious practices into its manufacturing processes, VSC is working with Carbon Conversions to reclaim, recycle and reuse its carbon fiber materials.
Switching from prepreg to RTM led to significant time and cost savings for the manufacture of fiberglass struts and complex carbon fiber composite foils that power ORPC’s RivGen systems.
Sara Black’s 2015 report on the development of snap-cure epoxies for automotive manufacturing still resonates today.
JEC World 2024: The Alliance for European Flax-Linen & Hemp is hosting an extended Natural Fibre Village, in addition to its latest work with the ecoinvent materials database and a conference session.
Automated fiber placement develops into more compact, flexible, modular and digitized systems with multi-material and process capabilities.
Available as filament and granules for extrusion, new wood composite matches properties yet is compostable, eliminates microplastics and reduces carbon footprint.
A recent study conducted on vacuum-infused thermoplastic fiber-metal laminates has highlighted the performance benefits behind using TFP’s nonwovens for consistent, uniform bondlines and interfacial bonding.
Switching from prepreg to RTM led to significant time and cost savings for the manufacture of fiberglass struts and complex carbon fiber composite foils that power ORPC’s RivGen systems.
Sara Black’s 2015 report on the development of snap-cure epoxies for automotive manufacturing still resonates today.
JEC World 2024: Zünd is highlighting digital excellence via its ZCC Cut Center, heat sealing module (HSM), G3 Cutter and ZPC software.
CW explores key composite developments that have shaped how we see and think about the industry today.
Knowing the fundamentals for reading drawings — including master ply tables, ply definition diagrams and more — lays a foundation for proper composite design evaluation.
As battery electric and fuel cell electric vehicles continue to supplant internal combustion engine vehicles, composite materials are quickly finding adoption to offset a variety of challenges, particularly for battery enclosure and fuel cell development.
Performing regular maintenance of the layup tool for successful sealing and release is required to reduce the risk of part adherence.
Increasingly, prototype and production-ready smart devices featuring thermoplastic composite cases and other components provide lightweight, optimized sustainable alternatives to metal.
The composite pressure vessel market is fast-growing and now dominated by demand for hydrogen storage.
The burgeoning advanced air mobility (AAM) market promises to introduce a new mode of transport for urban and intercity travelers — particularly those who wish to bypass the traffic congestion endemic to the world’s largest cities. The electric vertical take-off and landing (eVTOL) aircraft serving this market, because they depend on battery-powered propulsion, also depend on high-strength, high-performance composite structures produced at volumes heretofore unseen in the aerospace composites industry. This CW Tech Days will feature subject matter experts exploring the materials, tooling and manufacturing challenges of ramping up composites fabrication operations to efficiently meet the demands of a challenging and promising new marketplace.
Manufacturers often struggle with production anomalies that can be traced back to material deviations. These can cause fluctuations in material flow, cooling, and cure according to environmental influences and/or batch-to-batch variations. Today’s competitive environment demands cost-efficient, error-free production using automated production and stable processes. As industries advance new bio-based, faster reacting and increased recycled content materials and faster processes, how can manufacturers quickly establish and maintain quality control? In-mold dielectric sensors paired with data analytics technology enable manufacturers to: Determine glass transition temperature in real time Monitor material deviations such as resin mix ratio, aging, and batch-to-batch variations throughout the process Predict the influence of deviations or material defects during the process See the progression of curing and demold the part when the desired degree of cure, Tg or crystallinity is achieved Document resin mix ratios using snap-cure resins for qualification and certification of RTM parts Successful case histories with real parts illustrate how sensXPERT sensors, machine learning, and material models monitor, predict, and optimize production to compensate for deviations. This Digital Mold technology has enabled manufacturers to reduce scrap by up to 50% and generated energy savings of up to 23%. Agenda: Dealing with the challenge of material deviations and production anomalies How dielectric sensors work with different composite resins, fibers and processes What is required for installation Case histories of in-mold dielectric sensors and data analytics used to monitor resin mixing ratios and predict potential material deviations How this Digital Mold technology has enabled manufacturers to optimize production, and improve quality and reliability
SolvaLite is a family of new fast cure epoxy systems that — combined with Solvay's proprietary Double Diaphragm Forming technology — allows short cycle times and reproducibility. Agenda: Application Development Center and capabilities Solutions for high-rate manufacturing for automotive Application examples: battery enclosures and body panels
OEMs around the world are looking for smarter materials to forward-think their products by combining high mechanical performance with lightweight design and long-lasting durability. In this webinar, composite experts from Exel Composites explain the benefits of a unique continuous manufacturing process for composites profiles and tubes called pull-winding. Pull-winding makes it possible to manufacture strong, lightweight and extremely thin-walled composite tubes and profiles that meet both demanding mechanical specifications and aesthetic needs. The possibilities for customizing the profile’s features are almost limitless — and because pull-winding is a continuous process, it is well suited for high volume production with consistent quality. Join the webinar to learn why you should consider pull-wound composites for your product. Agenda: Introducing pull-winding, and how it compares to other composite manufacturing technologies like filament winding or pultrusion What are the benefits of pull-winding and how can it achieve thin-walled profiles? Practical examples of product challenges solved by pull-winding
Composite systems consist of two sub-constituents: woven fibers as the reinforcement element and resin as the matrix. The most commonly used fibers are glass and carbon, which can be processed in plane or satin structures to form woven fabrics. Carbon fibers, in particular, are known for their high strength/weight properties. Thermoset resins, such as epoxies and polyurethanes, are used in more demanding applications due to their high physical-mechanical properties. However, composites manufacturers still face the challenge of designing the right cure cycles and repairing out-of-shelf-life parts. To address these issues, Alpha Technologies proposes using the encapsulated sample rheometer (premier ESR) to determine the viscoelastic properties of thermosets. Premier ESR generates repeatable and reproducible analytical data and can measure a broad range of viscosity values, making it ideal for resins such as low viscous uncured prepreg or neat resins as well as highly viscous cured prepregs. During testing, before cure, cure and after cure properties can be detected without removing the material from the test chamber. Moreover, ESR can run a broad range of tests, from isothermal and non-isothermal cures to advanced techniques such as large amplitude oscillatory shear tests. During this webinar, Alpha Technologies will be presenting some of the selected studies that were completed on epoxy prepreg systems utilizing ESR and how it solves many issues in a fast and effective way. It will highlight the advantages of this technique that were proven with the work of several researchers. Moreover, Alpha Technologies will display part of these interesting findings using the correlations between the viscoelastic properties such as G’ and mechanical properties such as short beam shear strength (SBS).
Surface preparation is a critical step in composite structure bonding and plays a major role in determining the final bonding performance. Solvay has developed FusePly, a breakthrough technology that offers the potential to build reliable and robust bonded composite parts through the creation of covalently-bonded structures at bondline interface. FusePly technology meets the manufacturing challenges faced by aircraft builders and industrial bonding users looking for improved performance, buildrates and lightweighting. In this webinar, you will discover FusePly's key benefits as well as processing and data. Agenda: Surface preparation challenges for composite bonding FusePly technology overview Properties and performance data
Venue ONLY ON-SITE @AZL Hub in Aachen Building Part 3B, 4th Floor Campus Boulevard 30 52074 Aachen Time: January 31st, 2024 | 11:00-16:00h (CET) This first constitutive session will shape the future of the workgroup. ✓ Insights into solutions for e.g. circularity, recycling, sustainability, end of life etc. ✓ Interactive exchange along the value chain to tackle these challenges: Share your input in the “World Café” workshop session! ✓ Are you a solution provider? Take your chance and present your solution approach in a short 5-minute pitch. Get in touch with Alexander.
The Transformative Vertical Flight (TVF) 2024 meeting will take place Feb. 6–8, 2024 in Santa Clara, California, in the heart of Silicon Valley and will feature more than 100 speakers on important progress on vertical takeoff and landing (VTOL) aircraft and technology.
The EPTA – European Pultrusion Technology Association in cooperation with the American Composites Manufacturers Association (ACMA) invites you to the 17th World Pultrusion Conference which takes place on 29 February – 1 March 2024 in Hamburg, Germany. Visit the most important event in Europe in the market for pultruded fiber reinforced materials This conference takes place every two years and is the meeting point of the European and worldwide Pultrusion Industry. More than 25 international speakers from Finland, Belgium, Germany, France, Spain, The Netherlands, Turkey, UK, USA, Canada and others will present practical presentations about innovative applications, technologies and processes. Equally current market trends and developments are on the agenda. This World Pultrusion Conference takes place again in the week before the JEC World Composites Show (5-7 March 2024, Paris). The presentation language will be English. Please finde here the full program and booking opportunities. We appreciate very much welcoming you in Hamburg! Inquiries should be requested by email: info@pultruders.com
The Program of this Summit consists of a range of 12 high-level lectures by 14 invited speakers only. Topics are composite related innovations in Automotive & Transport, Space & Aerospace, Advanced Materials, and Process Engineering, as well as Challenging Applications in other markets like Architecture, Construction, Sports, Energy, Marine & more.
JEC World in Paris is the only trade show that unites the global composite industry: an indication of the industry’s commitment to an international platform where users can find a full spectrum of processes, new materials, and composite solutions.
Charting the Skies of Tomorrow: The Sustainable Aviation Revolution Welcome to a new era of air travel where innovation meets sustainability. Electric, hybrid-electric and hydrogen-powered aircraft represent a promising path to reach climate neutrality goals, with the aviation industry and governments jointly pushing boundaries to bring disruptive aircraft into service by 2035. From cutting-edge technologies to revamped regulations and greener airports, the pursuit of sustainable aviation requires unparalleled collaboration throughout the whole aviation value chain and ecosystem. Join us at the Clean Aviation Annual Forum from 5 until 6 March 2024, as we navigate towards cleaner skies together.
Thousands of people visit our Supplier Guide every day to source equipment and materials. Get in front of them with a free company profile.
Jetcam’s latest white paper explores the critical aspects of nesting in composites manufacturing, and strategies to balance material efficiency and kitting speed.
Arris presents mechanical testing results of an Arris-designed natural fiber thermoplastic composite in comparison to similarly produced glass and carbon fiber-based materials.
Cevotec, a tank manufacturer, Roth Composite Machinery and Cikoni, have undertaken a comprehensive project to explore and demonstrate the impact of dome reinforcements using FPP technology for composite tanks.
Initial demonstration in furniture shows properties two to nine times higher than plywood, OOA molding for uniquely shaped components.
The composite tubes white paper explores some of the considerations for specifying composite tubes, such as mechanical properties, maintenance requirements and more.
Foundational research discusses the current carbon fiber recycling landscape in Utah, and evaluates potential strategies and policies that could enhance this sustainable practice in the region.
As the marine market corrects after the COVID-19 upswing, the emphasis is on decarbonization and sustainability, automation and new forms of mobility offering opportunity for composites.
Novel material to combine Ohoskin’s leather alternative made from orange and cactus byproducts with ReCarbon’s recycled carbon fiber.
The three-year strategic collaboration will help boost the company’s growth, reinforce its commitments to become carbon neutral by 2040 and innovate more circular chemicals and materials.
Oak Ridge National Laboratory's Sustainable Manufacturing Technologies Group helps industrial partners tackle the sustainability challenges presented by fiber-reinforced composite materials.
Eco-friendly carbon fiber slashes carbon footprint by half through renewable energy, a commitment echoed in SGL’s Lavradio biomass plant set to reduce CO2 emissions by 90,000 tons.
JEC World 2024: Flax fiber producer Groupe Depestele and sustainable composites company Greenboats demonstrate flax fiber materials, demonstrators and product offer Circular Structures.
Closed mold processes offer many advantages over open molding. This knowledge center details the basics of closed mold methods and the products and tools essential to producing a part correctly.
In the Automated Composites Knowledge Center, CGTech brings you vital information about all things automated composites.
During CW Tech Days: Thermoplastics for Large Structures, experts explored the materials and processing technologies that are enabling the transition to large-part manufacturing.
Explore the cutting-edge composites industry, as experts delve into the materials, tooling, and manufacturing hurdles of meeting the demands of the promising advanced air mobility (AAM) market. Join us at CW Tech Days to unlock the future of efficient composites fabrication operations.
This CW Tech Days event will explore the technologies, materials, and strategies that can help composites manufacturers become more sustainable.
CompositesWorld’s CW Tech Days: Infrastructure event offers a series of expert presentations on composite materials, processes and applications that should and will be considered for use in the infrastructure and construction markets.
CW’s editors are tracking the latest trends and developments in tooling, from the basics to new developments. This collection, presented by Composites One, features four recent CW stories that detail a range of tooling technologies, processes and materials.
The composites industry is increasingly recognizing the imperative of sustainability in its operations. As demand for lightweight and durable materials rises across various sectors, such as automotive, aerospace, and construction, there is a growing awareness of the environmental impact associated with traditional composite manufacturing processes.
CompositesWorld’s CW Tech Days: Infrastructure event offers a series of expert presentations on composite materials, processes and applications that should and will be considered for use in the infrastructure and construction markets.
Explore the cutting-edge composites industry, as experts delve into the materials, tooling, and manufacturing hurdles of meeting the demands of the promising advanced air mobility (AAM) market. Join us at CW Tech Days to unlock the future of efficient composites fabrication operations.
Thermoplastics for Large Structures, experts explored the materials and processing technologies that are enabling the transition to large-part manufacturing.
Explore the technologies, materials, and strategies that can help composites manufacturers become more sustainable.
A report on the demand for hydrogen as an energy source and the role composites might play in the transport and storage of hydrogen.
This collection features detail the current state of the industry and recent success stories across aerospace, automotive and rail applications.
This collection details the basics, challenges, and future of thermoplastic composites technology, with particular emphasis on their use for commercial aerospace primary structures.
This collection features recent CW stories that detail a range of tooling technologies, processes and materials.
Versatile sandwich panel technology solves decades-long exterior automotive challenge.
RLE International developed an innovative, low-cost/low-pressure compression molding variant and thermoplastic sandwich panel technology that has been in production on the interior bulkhead (above) of a commercial vehicle since 2019. The technology is now being investigated to produce exterior roof panels and hoods. Photo Credit: SABIC
For at least five decades, significant work across the global automotive composites supply chain has focused on trying to make thermoplastic composites a viable option for horizontal body panels with a Class A finish, including hoods, roofs and decklids (trunk lids). (Below, sidebar A provides a short history of composite body panels and sidebar B discusses why this is desirable.) Thermoset composites replaced metals on vehicle exteriors in semi-structural/vertical and fully structural/horizontal body panels starting in the 1950s. Thermoplastic composites have been used intermittently on vertical body panels like bumper fascia and fenders since the 1980s, door panels and other trim since the 1990s and liftgates since the early 2000s. However, it has proven difficult to meet the auto industry’s performance, cost and aesthetic requirements in horizontal panels with this class of materials.
Illustrated by Susan Kraus. Original image credit: RLE International
That may be changing thanks to a low-pressure variant on compression molding and thermoplastic sandwich panel technology out of the U.K. For 4 years, the technology has been in production on a large bulkhead for a light commercial vehicle rated to carry 2 tonnes of cargo. More recent work, which is discussed here, suggests the technology may offer the right combination of design flexibility, mechanical performance, affordable and rapid processing and surface aesthetics to be viable on horizontal exterior panels at last.
Eight generations of the composite-bodied Chevrolet Corvette sports car from General Motors Co. highlights an interesting progression of composite materials used for body panels. Photo Credit: General Motors Co.
Thermoset composites have a long history of use on passenger vehicles for semi-structural vertical and fully structural horizontal exterior body panels as well as chassis/monocoque elements. Glass fiber-reinforced plastic (GFRP) debuted in 1953 on all exterior panels of the new Chevrolet Corvette sports car from then General Motors Corp. (now General Motors Co., GM, Detroit, Mich., U.S.). In the 1960s, hand layup FRP was replaced with faster cycling and more consistent compression molded sheet molding compound (SMC) on the Corvette. Since then, SMC’s use has expanded beyond body panels to encompass structural pickup boxes, chassis components and, more recently, large protective enclosures for electric vehicle battery packs (read CW’s Part 1 and Part 2 articles on this application). Additionally, carbon fiber/thermoset matrix composites transitioned from significant portions of Formula 1 and 2 race cars in the 1990s to body panels and later, entire monocoques of street-legal cars (including the Corvette) starting in the early 2000s.
Injection molded short glass fiber-reinforced thermoplastics debuted on non-structural bumper fascia in the early 1980s and by the mid-1980s were transitioning to other vertical panels like fenders. In 1990, when GM’s Saturn cars debuted, all vertical body panels were injection molded thermoplastic composite. However, the hood, decklid and roof stayed in stamped steel and eventually the entire exterior body transitioned to steel before production ended in 2010.
Several other GM nameplates sported thermoplastic vertical panels that decade, as did vehicles like the limited-edition (1989-1991) Z1 roadster from BMW AG (Munich, Germany) and later the diminutive smart fortwo micro car that then Mercedes-Benz division of Daimler AG (now Mercedes-Benz AG, Stuttgart, Germany) launched in 1997. Smart was the first car to feature all thermoplastic body panels, although hood and roof panels were very small indeed. In 2007, smart became the first passenger car to switch from fiberglass-reinforced polycarbonate/polybutylene terephthalate (GR/PC-PBT) to talc-filled thermoplastic polyolefin (TPO).
Over the last 15 years, talc-filled TPOs have slowly displaced engineering thermoplastics like GR/PC-PBT and GR/modified-polyphenylene ether-polyamide (GR/MPPE-PA) on vertical body panels. Another significant milestone that was 10 years in the making occurred in 2014 with the debut of an all-thermoplastic liftgate (a talc/TPO outer panel bonded to a long fiber thermoplastic polypropylene (LFT-PP) inner panel) on Nissan Rogue cross-over utility vehicles (CUVs). Since then, other SUVs and CUVs have followed suit.
The story begins circa 2015 when an automaker’s engineering team approached the U.K. offices of RLE International (Cologne, Germany) for help taking cost and mass out of a commercial vehicle. RLE is internationally known for its automotive design and engineering work, particularly on primary body structures and interiors. As such, the company provides full CAE, engineering, styling feasibility and launch support. RLE’s team proposed several metal-to-composite conversion options to reduce cost and mass, including fully structural/horizontal exterior roof panels and a semi-structural/vertical interior bulkhead between cabin and cargo hold.
The joint team tackled the technically easier bulkhead first. Over the next few years, design of the bulkhead evolved such that the technology eventually passed all OEM performance requirements. To meet the OEM’s maximum 12-kilonewton impact requirement, the final bulkhead features skins of a single layer of lightweight reinforced thermoplastic (LWRT)— comprising a polypropylene (PP)-impregnated loftable, short glass, low grams/square-meter (GSM) form of glass mat thermoplastic (GMT) composite material — sandwiching a core of 0°/90° unidirectional (UD) fiberglass tapes (although fabric weaves also could be used). The LWRT skin materials were selected to provide a good unpainted surface finish.
Bulkheads are molded in <90 seconds via a low-cost/low-pressure (3.4-4.5 bar) “thermopressing/consolidation” variant on compression molding in matched metal dies at room temperature. The tool is neither heated nor chilled, but materials used in the sandwich structure are preheated before forming. Since the tool doesn’t have a shear edge, waterjet trimming is required after demolding to clean up the part edge and cut any required holes. The one-piece panel replaced a multipiece steel/polyurethane foam liner assembly, reduced mass by 5.2 kilograms, lowered piece cost and decreased tooling investment by 80%. Additionally, the all-fiberglass/olefin sandwich structure is fully recyclable at end of part life. Commercial since 2019, the award-winning bulkhead is produced in volumes of 60,000-70,000/year, although reportedly, the process can produce up to 90,000 parts/year from a single tool.
Believing that the same technology would work for an external roof panel, RLE’s team — led by Mark Grix, head of interior/exterior development — opted to move forward on its own to develop a Class A-capable horizontal roof panel. Grix has developed thermoplastic exterior body panels since his days at GE Plastics in the 1990s.
Since the team had a modest budget, clever approaches were needed. One such approach involved obtaining three free exterior steel roof panels — intended for use as the outer/skin layer of welded roof panels on the same commercial vehicle that sports the bulkhead. The panels did double duty. One was scanned and used to create a template to rapidly design the panel’s outer skin, significantly reducing CAE time. Since the interior (B-side) of the roof panel wasn’t part of the proof of concept, the team focused solely on exterior (A-side) geometry and surface finish.
The other two steel panels were used to create a low-cost forming tool, with one skin functioning as the core and the other as the cavity to mold the A and B surfaces of the relatively flat composite roof panel. The roof tool was subsequently used to form composite panels during the development program and Grix says it produced excellent parts right from the start.
Beginning with a sandwich structure similar to that used for the commercial bulkhead, a number of different combinations of skins and cores (in total thicknesses ranging from 3 to 5 millimeters) were laid up, molded and evaluated to develop the roof panel concept. Once the various materials were preheated (different layers may be subjected to heat for different lengths of time), they were manually laid up in a compression press loaded with the aforementioned tool (held at room temperature) and formed via thermopressing. Researchers again targeted an effective cycle time of 90 seconds.
Working without OEM specs for the developmental roof panel, RLE focused its efforts on the exterior skin, with the intention of keeping roof hoops/bows in place and bonding the composite solution to an existing weld flange used for the current metallic roof. This was possible because the composite structure was formulated to have a low coefficient of linear thermal expansion (CLTE). Subsequent testing has shown the target thermoplastic panel has a CLTE close to that of aluminum. Photo Credit: RLE International
Roof panels were molded at a U.K. facility owned by Airborne (The Hague, Netherlands) in order to further develop the concept and achieve the right combination of skins and cores for the sandwich panel construction. Airborne’s facility was ideal, since it was equipped with a very large oven capable of heating the entire 1.75 × 2.0-meter roof panel and could heat materials to 240°C. Ironically, the oven actually proved too large for the panel and work was done to section off part of the oven so material didn’t have too long of a dwell time, and to permit material to be fed in from the side partway down the length of the oven rather than from the end.
Various combinations of panel materials were subsequently subjected to small-scale lab tests. Eventually, the most promising candidate was bonded — via 1K structural urethane adhesive from Sika AG (Baar, Switzerland) — onto the roof hoops/bows of a test vehicle and subjected to additional vehicle-level testing.
Since the final composite is assembled in the press just before consolidation and forming, depending on the desired properties and surface finish required for an application, RLE’s technology offers great versatility regarding the types of materials that can be combined to form the final panel’s skins, cores and exterior surface finish. Nearly any type of sheet-form thermoplastic composite can be used (e.g., tapes, GMT, organosheet, LWRT). The only requirements are that polymer matrices be chemically compatible (to achieve good material flow, ensuring a homogeneous component), and have similar glass transition temperatures (Tg) to permit heating in the same oven without worrying that higher temp materials will melt lower temp ones before consolidation/forming is complete.
“Every application’s requirements are going to be different, so we have the flexibility to work with materials with FVFs [fiber volume fractions] ranging from a high 20% to the 50% range, although we typically like to come in around 30-40%,” explains Grix. “Testing has shown us there’s no benefit to be gained by using higher FVFs. And, in fact, if we have too much glass [to resin], then impact strength and adhesion between layers suffers. To get a good surface, it is absolutely essential to have enough resin.”
For the top-most aesthetic layer, which controls surface finish, candidates include matte or gloss thermoplastic films, textiles, scrim/fabric combinations or even scratch/UV-resistant hardcoats or soft-touch thermoplastic polyurethane (TPU) coatings. Again, the beauty of the technology is that it can easily be modified on-the-fly to meet application needs in many industries.
To date, RLE has produced automotive Class A-capable panels in durable and UV-resistant gloss or matte surfaces directly from the mold using precolored films and low-cost aluminum tooling in a cycle time of <2 minutes. Compared to steel panels, composites offer a potential mass savings of 50% for structural panels and 60% for exterior/semi-structural panels. They also offer excellent impact strength even at low temperatures and full end-of-life recyclability. This thermoplastic sandwich panel technology is gaining interest among not just automotive industry players, but also those in other ground transportation segments. Photo Credit: RLE International
The team looked at different combinations of thermoplastic resin systems (primarily in the olefin and polyamide families) and reinforcements (including chopped, UD and woven fabrics) for the skins and cores of the roof’s sandwich panel. Owing to its elevated position, the developmental roof panel didn’t require a Class A finish. Initially, precolored black material was used and matte white panels were also tried. More recently, Grix and his team have improved UV stability and scratch resistance by applying a film layer in the tool as well as trying a hardcoat finish. The panel can use a contrast color or it can match the rest of the body. No metallic reinforcements are required in either the developmental roof panel or the commercial bulkhead. Should the entire steel roof — not just a single panel — be converted to the thermoplastic sandwich technology, Grix estimates a mass savings of 24.5 kilograms could be achieved.
A big question automakers like to ask is what technology readiness level (TRL) a concept currently is at, and Grix’s answer is that the roof panel concept is fairly far along.
“You’ll still need to do some OEM-specific testing, like environmental stability, NVH [noise/vibration/harshness], and things like that, but for all intents and purposes, the roof panel uses the same material family and a variation of the same processing method as the bulkhead, which has been in fairly high-volume commercial production for the last four years,” he explains. “The flexibility of this technology means that if you need to increase UV performance or scratch resistance, or even to make the panel thicker or thinner or more rigid, then we can do that. We’ve spent a lot of time really working to understand this technology and what’s required to make nice panels right out of the tool.”
Another developmental project that RLE has investigated is using the thermopressing/sandwich panel technology to produce a hood. In this case, the outer panel used a higher temperature polyphthalamide (PPA) matrix. Again, the team found mass savings greater than 50% versus steel and excellent PedPro performance in a recyclable panel. Photo Credit: RLE International
RLE reportedly is in discussions with automotive Tier 1s and OEMs in other ground transportation segments like farm equipment and golf carts to commercialize both interior and exterior applications.
What’s next for this technology? “There’s no reason (with the right formulation) this technology can’t be used for PedPro- [pedestrian protection] compliant hoods too,” Grix says. “We’ve already produced a developmental hood, and small-scale testing shows we have better energy absorption and dissipation than thermosets or steel. Also, we’ve explored using this technology not just for relatively simple panels but for high-draw panels for vehicle interiors with significantly more geometric complexity. Combine that with a Class A precolored finish right out of the tool, mass savings of 50-60% versus steel and a fully recyclable part at end of life and we feel this is a winning combination for OEMs looking for lightweight panel technologies in multiple industries. We’d love to work with anyone interested in exploring this further.”
Compared to either thermoset composites or metals, thermoplastic composites are desirable for exterior body panels for many reasons. First, they tend to be lighter (lower specific gravity), they have better damage tolerance (impact strength) — a bonus for meeting PedPro requirements — and they provide better surfaces out of the tool, reducing post-mold finishing.
Unlike thermosets, thermoplastic composites are recyclable (melt reprocessable), making it easier to reuse scrap and recover usable material from end-of-life parts — an important feature for those selling vehicles into the EU — and they’re also supplied fully polymerized, meaning molding cycles tend to be shorter and offer better repeatability and reproducibility (R&R), which makes them better suited for higher volume programs and helps offset their typically higher raw material and tooling costs. They also offer greater design freedom and ample opportunities for parts integration (to reduce part count), insertion of hardware (to facilitate joining) and simplified post-mold assembly versus metals.
Despite all their benefits, thermoplastic composites — like all materials — have challenges that must be overcome. For example, owing to higher CLTEs than steel or aluminum, early monolithic thermoplastic composite body panels with discontinuous fiber reinforcement required that larger-than-desirable gaps be left between composite and metallic panels to accommodate dimensional changes during temperature cycling. Without this aesthetic tradeoff, moveable panels like doors couldn’t be opened or closed at times. That has largely been overcome by switching from monolithic panels to pairs of bonded inner/outer panels — with or without cores — and by using longer chopped/discontinuous fiber reinforcement as well as continuous fiber nonwoven, unidirectional and woven reinforcements in sheet form composites like GMT/organosheet and thermoplastic tapes.
Another problem was that the thermoplastic grades the automotive industry favors — largely PP, PA 6 or 6/6 and blends of PA or thermoplastic polyester with PC or MPPE — lacked thermal stability to endure bake oven temperatures after electrophoretic coating (e-coat) of the body-in-white (BIW) and painting. That added assembly complexity and cost, since panels had to be painted offline and added at a later stage in the vehicle assembly process. Although painting of thermoplastic panels is still accomplished offline, much work has been done to improve the UV stability, depth-of-color and metallic special effects of molded-in-color (MIC) panels, which then only require a clear coat to finish. Additionally, great strides have been made in film technology, which offers more durable surfaces than paint and aligns with automaker efforts to reduce the cost and environmental burden of painting.
Still another formulating problem was striking the right balance between stiffness and impact to avoid the need for large metallic brackets on which vertical panels hang from the vehicle. A related issue is that since stiffness and strength are often lower than values for metals, geometry (such as ribbing) was often needed to achieve comparable mechanical performance in panels. That, however, tended to lead to thicker nominal walls, which can cause packaging issues. Faced with the prospect of having to redesign body structures on existing vehicles to accommodate thicker composite panels, most OEMs will just pass. For TPO materials, careful formulation work that combines both discontinuous fiber reinforcement and mineral fillers has led to these materials dominating skins on exterior vertical panels. Also, by switching from a monolithic panel design to a bonded inner/outer panel, a structural inner panel that wouldn’t meet Class A requirements is complemented by a Class A-capable outer skin that wouldn’t meet mechanical requirements alone.
Perhaps the greatest challenge that made thermoplastic horizontal panels unviable for decades was the issue of sagging and long-term creep at elevated temperatures. There were several reasons for this. First, thermoplastics soften over a range of temperatures close to their Tg, which causes a progressive loss of mechanicals including the ability to carry loads and be self-supporting. The property that makes them easier to recycle can also compromise their long-term mechanical integrity at elevated temperatures. To an extent, that is helped by switching from short/discontinuous fiber reinforcement to continuous fiber options, and moving from monolithic panels to bonded panels with or without cores.
A related issue is how to achieve sufficiently high FVFs or FWFs to improve mechanicals during periods of elevated temperatures. The fact that thermoplastic polymers are supplied prepolymerized (with very long molecular chains before molding) means that even at melt temperatures, they are fairly viscous compared with many liquid thermoset systems. That makes it hard to achieve high levels of fiber wetout and impregnation. Hence, even today, there are limited injection molding grades with FWFs above 40%, whereas many thermoset technologies permit FVFs as high as 70% to be achieved. To an extent, this has been addressed by a combination of careful resin selection (e.g., using branched versus linear forms of PP with lower viscosity), modifications to the lamination process for thermoplastic tape and GMT/organosheet production and, more recently, impregnation with low-viscosity caprolactam monomer that is subsequently reactively polymerized into PA6. The tradeoff is longer cycle times (more like thermosets) and specialized equipment. However, the increasing ability over time to get more fiber, particularly more long and continuous fiber, into thermoplastic composites has been a great enabler for their use in increasingly structural applications. The one tradeoff here is that for exterior aesthetic surfaces, higher FVFs/FWFs can lead to fiber readthrough. This can be addressed, in part, by using films, by painting or texturing the panels or by using lower fiber reinforcement in the outermost aesthetic layers in sandwich panel compositions.
Last but not least, direct and indirect costs are always a sensitive point in the high-volume/low-margin automotive industry. While the composites industry was working on material and process advancements to address one body panel challenge after another, so too did counterparts in the aluminum and steel industries improve their materials and processes. Even today, unless switching to composites permits significant mass to be removed from a vehicle, provides important manufacturing benefits or enables new levels of safety or functionality to be added, most automakers will balk at using composites unless the cost to do so is at least neutral or lower than that of conventional materials.
Shocker Composites and R&M International are developing a supply chain for recycled CF with zero knockdown vs. virgin fiber, lower cost and, eventually, lengths delivering structural properties close to continuous fiber.
Although the long-anticipated market surge in basalt fiber-reinforced polymer composites remains largely in the future, basalt fiber manufacturers are making headway over the technical and market hurdles toward large-scale application.
The matrix binds the fiber reinforcement, gives the composite component its shape and determines its surface quality. A composite matrix may be a polymer, ceramic, metal or carbon. Here’s a guide to selection.
Compared to legacy materials like steel, aluminum, iron and titanium, composites are still coming of age, and only just now are being better understood by design and manufacturing engineers. However, composites’ physical properties — combined with unbeatable light weight — make them undeniably attractive.
Glass fiber/foam preform technology is key to the all-composite refrigerated truck body panels.
Hybrid structural-reinforcement technology expands options, gains applications, markets.
Side story to Composites in Class A body panels: Evolution continues.
Starting on Tuesday, Jan. 23, 2024, CW will begin “gating” its staff-produced premium content, asking all new website users to provide some information about themselves — name, title, employer, email address — before they are provided free access to the content.
We are doing this because the ways CW’s audience finds and accesses our content is changing. Google’s search algorithms, increasingly, make it difficult to connect CW’s content with the people who might make use of it. On top of that, generative AI like ChatGPT is serving up CW content to internet users without attributing that content to CW.
As a result, it has become increasingly important for CW evolve its audience development strategy and learn as much as possible about who is accessing our content, what content they are accessing and how they are accessing it.
With this audience development strategy, we hope to do two things:
CW plays a distinctive role and has earned a place of esteem within the focused and specialized industry it serves. Large developments in the media landscape are forcing us to change the way we communicate with our audience. We are confident that our audience values the role CW plays in their professional lives and will join us in this effort to stay connected to them
We thank you for your continued interest in and support of CW and welcome any questions you might have about the brand’s new content gating strategy.
Unlimited access to our free premium content requires a little more information from you.
Your email address will be used to communicate with you about CompositesWorld subscription offers, related products and services. Refer to our Privacy Policy for more information. Wondering why you’re seeing this? Read more here.

Aluminium Clean Room Panels CompositesWorld is the source for reliable news and information on what’s happening in fiber-reinforced composites manufacturing. Learn More