The complexity and costs of drilling modern wellbores constantly challenge the design of roller cone and fixed cutter drill bits. Durability and penetration rates continue to be key areas of focus as the means to improve drilling economics and performance.
Achieving these fundamental objectives requires continuous improvements that keep pace or lead advancing capabilities in drilling technology. Recent challenges include rotary steering systems that place greater wear loads on the side of the bit and complex drilling applications where high durability is required. Bit technology must also address the economics of costly drilling operations that place increasingly high premiums on speed, reducing risk and minimizing non-productive time. Gauge Polycrystalline Diamond Inserts
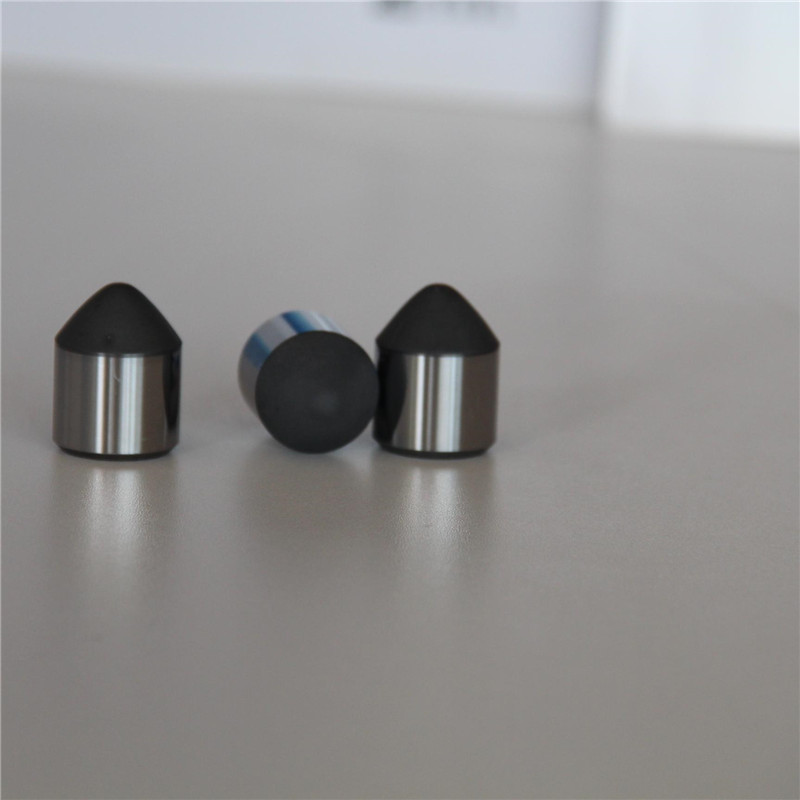
ReedHycalog, a new member of the Grant Prideco family, is advancing new roller cone designs that provide durability in the difficult applications. New fixed cutter designs benefit from significant material advances that keep the bit sharper, longer.
One of the most important dimensions in the advancement of fixed cutter bits is that of improving the cutting elements themselves. A new class of synthetic diamond cutter called TReX was designed and developed in-house at the facility in Stonehouse, UK, and made using three diamond presses.
The cutters feature an ultra wear-resistant, thermostable layer on the leading edge of the diamond table. In laboratory tests, this material is four times more abrasion resistant than even the highest-grade premium polycrystalline diamond compact (PDC). This wear resistance is achieved without any reduction in impact resistance, which has been the industry's traditional trade-off in PDC cutter design and manufacture.
As a TReX cutter wears, the ultra wear-resistant, thermostable layer forms a distinct lip that increases contact stress at the rock interface, providing typically 30% more rate of penetration than a premium PDC cutter bit.
The cutters can be fitted into any of ReedHy-calog's PDC bit bodies. They provide performance in any PDC application with no downside performance risk. The most significant increase in performance is achieved in very abrasive formations where conventional PDC bits are uneconomical. In these situations, bits equipped with these new cutters typically extend footage drilled by 30% and will drill formations not previously drillable with PDC bits.
Because the cutters are more abrasion resistant and maintain a sharp cutting edge during drilling, they enhance bit performance by staying sharper longer, so the bit drills farther and faster.
A 9 7/8-in. DSX147GVW fitted with these cutters provided substantial improvements to drilling performance in Live Oak County, Texas, in water-based mud. On one well this cutter bit drilled 5,710 ft in 49 hours. The average penetration rate was 116.5 ft/hr and the bit came out rated 1-1-WT-A-X-I-NO-KOP. The DSX147 more than doubled offset penetration rates while drilling a longer interval, clearly establishing the best PDC bit run in the area.
In Australia's Northwest Shelf, the cutters increased the footage drilled by 195% allowing the operator to complete an entire section in one trip. The 8 1/2-in DSX203 PDC bit drilled a total interval of 662 m at a record 28 m/h and was graded at 2-3-WT-A-X-I-CT-NO-TD. The sidetrack offset required two competitor bits to drill the interval at ROPs that were 55% slower.
The Triassic Ormskirk formation located in Morecambe Bay, UK, is a highly abrasive sandstone, which in the past caused operators to use diamond-enhanced insert bits. On one recent well a 404-ft section of this interval was drilled vertically with one 8 1/2-in. diamond enhanced insert bit at 27.7 ft/hr. On the sidetrack well a 6-in. DSX143DGJ TReX cutter bit drilled a total of 2,992 ft at 42.7 ft/hr. The bit built angle to 87°, followed by a 1,650-ft tangent. The original well design included one milltooth and five diamond enhanced insert bits for this sidetrack.
In Algeria, a study was completed with 6-in. bit runs. An analysis of a total of 54 bit runs revealed that the DSX143 fitted with these cutters drilled on average over 43% further and 33% faster than the best competitor average. This 6-in. fixed cutter bit is now the bit of choice in this application.
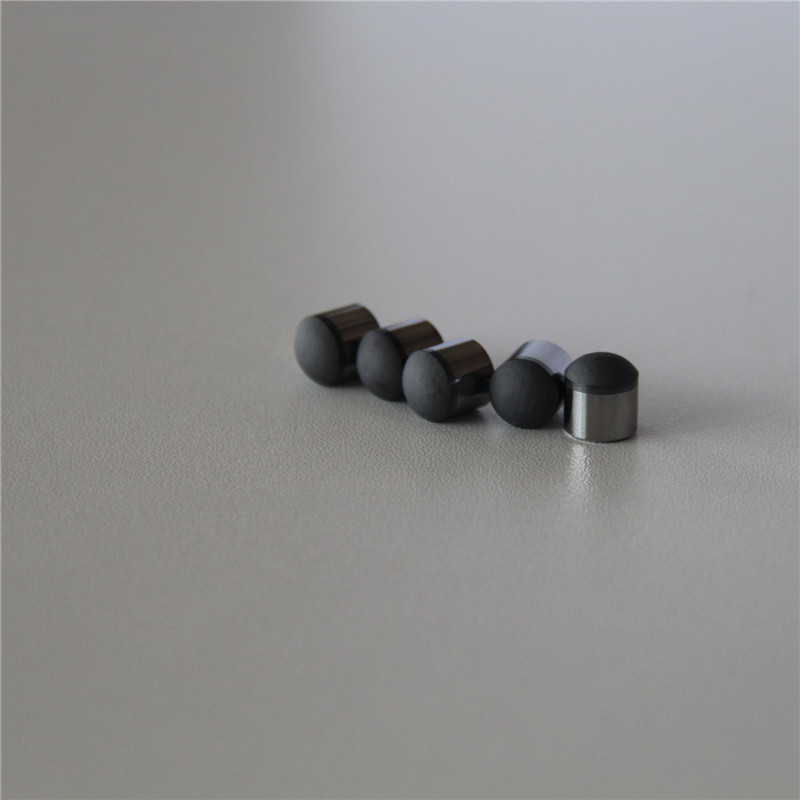
Mining Cutting Tools For information, contact the author at Greg.Petterson@ ReedHycalog.com.