CNC machining is a cost-effective production method when implemented effectively.
Ensuring that CNC machining is cost-effective, that it allows operation the best opportunity to meet its fullest potential requires complex decision-making. One of the most important of these decisions is selecting the right material for machining. Cnc Milling Turning Machining Aluminum Precision Parts
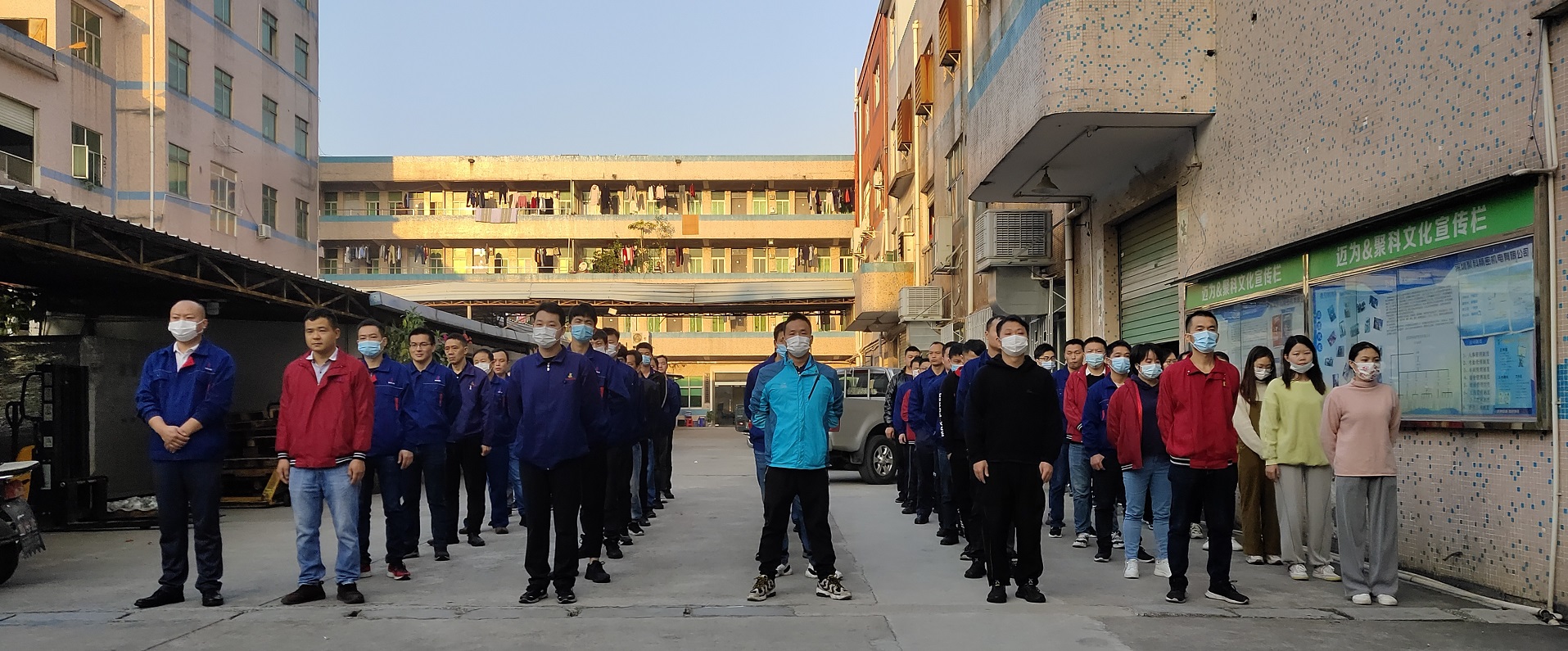
Many CNC optimization strategies look at the machinery, and that is an important aspect. However, material selection impacts cost-effectiveness in several different ways.
Material costs vary widely. The raw material costs metals can change dramatically depending on the specific metal you choose. As of September 2023, aluminum costs average just over $1 per pound , whereas copper is more than three times as much. And while copper is still relatively affordable, prices vary even more with higher-end metals like titanium.
A CNC machine’s cost-efficiency will only go so far with excessive raw material costs. Some metals also are prone to price volatility, making it difficult to estimate material expenses accurately over a longer period.
Varying machining requirements. Metal production costs include more than just the material’s upfront costs. Some metals are easier to machine than others, affecting the overall cost of manufacturing the product in question. In some cases, that may result in a more expensive raw material being more cost-effective to machine.
A material’s hardness and thermal conductivity are the biggest factors to consider, but other qualities impact the ease of machining, too. While aluminum’s malleability makes it easy to cut, its low melting point makes it susceptible to fusing and warping during high-intensity machining. Steel may be harder and more expensive upfront, but is more resistant to those issues.
Recyclability varies. Different CNC machining metals also carry varying recyclability ratings. Machining is a subtractive process, creating some scrap waste regardless of how accurate the cutting may be. However, if you’re using an easily recyclable metal, the chips or turnings may be recyclable to offset future raw materials costs.
U.S. manufacturers recycle 60% of the titanium they process but just 47% of steel and one-third of all copper. Consequently, while titanium costs more upfront, its high recycling rate makes it easier to find cheaper recycled sources. You can also recycle your own titanium scrap too, to drive costs down further.
Since metal selection can impact your costs in many ways, it takes careful planning to determine the best fit for your needs. Here’s how you can find the ideal CNC machining metal for you.
Determine product needs. The first step is to outline what material qualities your end product must have. The product may need to have high electrical conductivity — or none at all — to work properly, vastly narrowing your options. Similarly, some parts must meet specific strength or weight requirements.
Be sure to consider any application-unique needs your product may serve. If the metal will see use in outdoor environments, you should limit your search to metals with high corrosion resistance. Medical devices benefit from metals with antimicrobial properties. Serving the end user takes precedence over other factors, so determine these needs before finding ways to reduce costs.
Review equipment and workflows. You can further narrow your search by considering your CNC equipment and workflows. Five-axis machines are more efficient than conventional alternatives , allowing you to use tougher metals. Conversely, if you have slower or more error-prone equipment, you should favor more easily machinable materials.
It’s also important to consider any post-machining processes. Some metals are easier to plate than others. Using a corrosion-resistant alloy can remove the need for post-processing treatment. Review your workflows for steps like this to see where you can eliminate or streamline them with different materials.
Consider future changes. Keep in mind that machining metal costs will likely change over time. Metal values can fluctuate week to week , much more so over an entire year. Still, some material values shift more than others, and some changes are predictable, so it’s important to stay on top of these trends.
Finished products with higher profit margins can withstand more price volatility, but low-margin manufacturing should favor metals with more historically consistent prices. When selecting a metal for milling, turning, or other manufacturing process, you should also see how it might change in the future and consider these price shifts when calculating expenses.
Reduce costs elsewhere. After working through these selection steps, you may find your product and processes require a more expensive metal. If so, adjust the machining workflow to compensate for those high costs.
Designing for efficiency is one of the best solutions. Artificial intelligence (AI)-assisted generative design can recommend product changes to create similar structures that require less material. Some organizations have reduced part costs by up to 20% this way.
Cost-efficient machining starts with choosing the right material. When you know how material selection impacts your bottom line, you can make better decisions about your resources. Following these steps will help you find the right CNC machining metal for you to make excellent products while minimizing costs.

The Cnc Machining Emily Newton is the Editor-in-Chief of Revolutionized, an online magazine exploring the latest industrial innovations.