The $37 million contract will enable Piasecki to demonstrate its ARES tilt-duct VTOL aircraft and hydrogen fuel cell propulsion technologies.
Design Organization Approval makes Lilium qualified to design and hold a type certificate for aircraft developed according to the EASA’s SC-VTOL safety objective rules. Glass Fiber Weave
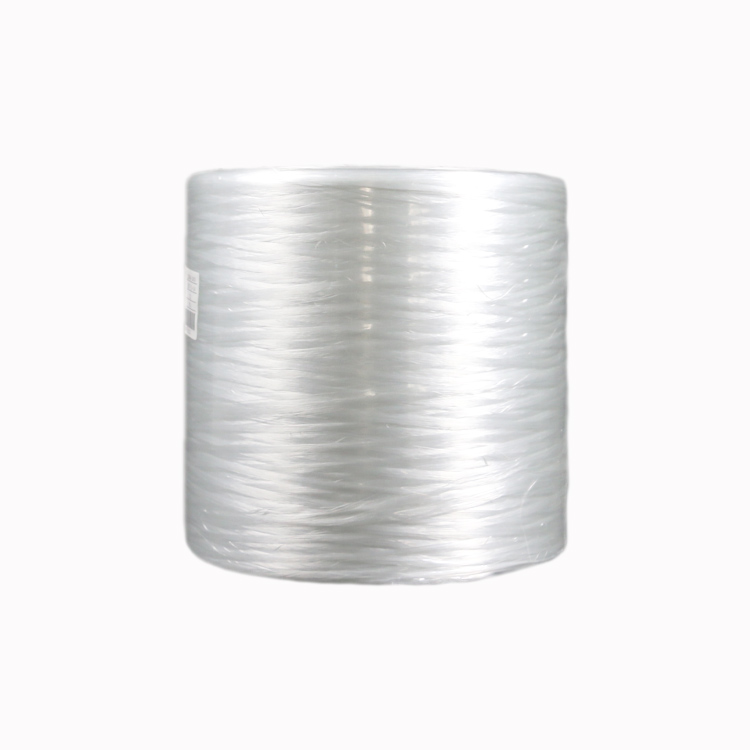
The two-seat EL-2 Goldfinch is a blown-lift aircraft filling the gap for air travel routes between 50-500 miles. Certification and entry into service is targeted for 2028.
The Spanish electric mobility solutions developer is steadily growing its team and investments, emphasized by its rebranding from Umiles Next and the introduction of Integrity to customers.
$9.8 million will grow the eVTOL aircraft manufacturer’s footprint in Marina, California, support 690 new state jobs and accelerate early manufacturing to support initial commercial operations, targeted for 2025.
Midnight aircraft will provide an opportunity to streamline everyday urban congestion challenges, in addition to other use cases.
Evaluation of CFRTP m-pipe through Element’s U.K. facility aims to qualify the system for new operating environments.
Innovative prepreg tooling is highly drapable, capable of forming complex carbon fiber tooling shapes, in addition to reducing through thickness porosity and only requiring one debulk during layup.
Simutence and Engenuity demonstrate a virtual process chain enabling evaluation of process-induced fiber orientations for improved structural simulation and failure load prediction of a composite wing rib.
3D imaging and analysis capability illustrates detailed, quality characterization and performance simulation of composites and other advanced materials that properly captures the as-manufactured component.
Latest version of comprehensive simulation software speeds up computations and introduces surrogate model functionality.
As part of its efforts to automate as much of its production process as it can, Lyons Industries acquired a Massivit 10000 additive manufacturing system to quickly produce high-performance molds and support fixtures.
Qarbon Aerospace will focus on the design, development and manufacture of a thermoplastic composite structure for defense aviation components requiring icing protection.
Fraunhofer IFAM researchers and partners combine biodegradable polymer polycaprolactone and bioactive glass to 3D print custom-fit structures for bone fracture sites.
The carbon fiber wheel manufacturer and supplier has been awarded a total of 18 vehicle programs over the last couple of years, and is now looking to build capacity.
Lehvoss’ carbon fiber-reinforced thermoplastic composite materials are being used in the production of an e-bike set that will taken an expedition across North Africa.
Through the use of EzCiclio low-dielectric epoxy hardener, PCB manufactures can make recyclable, reusable products for electronic applications.
Terrene 3.0 is a compression-dominant arch developed as a multidisciplinary research project composed of natural fiber-reinforced sand and other biomaterials that delivers eco-friendly, less energy-intensive building methods.
New developments regarding productivity, maintenance and ergonomics make this enhanced composite placement system well suited for the production of complex parts.
Data collected from one year of outdoor testing reasserts the 3D-printed, bio-based structure’s viability to address housing challenges, sets the stage for future development.
Using Mechnano’s D’Func process, the new masterbatch of ogolimers enables 3D printing resin development with improved mechanical and nano-uniform electrical performance.
Collins Aerospace draws on global team, decades of experience to demonstrate large, curved AFP and welded structures for the next generation of aircraft.
Discussion of the issues in our understanding of thermoplastic composite welded structures and certification of the latest materials and welding technologies for future airframes.
The open AM innovation program welcomes all interested parties who would like to make use of the potential of 3D printing FGF or combine it with materials like carbon fiber, UD tape and other hybrid technologies.
CW explores key composite developments that have shaped how we see and think about the industry today.
Knowing the fundamentals for reading drawings — including master ply tables, ply definition diagrams and more — lays a foundation for proper composite design evaluation.
As battery electric and fuel cell electric vehicles continue to supplant internal combustion engine vehicles, composite materials are quickly finding adoption to offset a variety of challenges, particularly for battery enclosure and fuel cell development.
Performing regular maintenance of the layup tool for successful sealing and release is required to reduce the risk of part adherence.
Increasingly, prototype and production-ready smart devices featuring thermoplastic composite cases and other components provide lightweight, optimized sustainable alternatives to metal.
Interest in higher performance and more sustainability drive new composite materials innovations in sporting goods and other consumer products.
ICERP India is an important event of the Indian composites industry organized by FRP Institute once in every two years and ICERP event is the biggest event on Composites in India and second biggest event in Asia.
The annual Conference on Composites, Materials, and Structures (also known as the Cocoa Beach Conference) is the preeminent export controlled and ITAR restricted forum in the United States to review and discuss advances in materials for extreme environments. The Conference started in the 1970s as a small informal gathering for government and industry to share information on programs and state-of-the-art technology. Attendance has grown to nearly 500 people while preserving this same objective to share needs and trends in high-temperature and extreme environment materials, and the latest information on advanced materials and manufacturing processes. The five-day conference program includes two to three parallel sessions per day on topics including thermal protection materials, ceramic matrix composites, carbon-carbon materials, ballistic technologies, hypersonics, and gas turbine engines. Attendees are engineers, scientists, managers, and operational personnel from the turbine engine, aviation, missiles and space, and protective equipment communities. These communities include the Navy, Air Force, Army, MDA, NASA, DARPA, FAA, DOE, engine manufacturers, missile and aircraft manufacturers, commercial space companies, and material and component suppliers. The Conference will be held in St. Augustine again for 2024! Participation is limited to U.S. Citizens and U.S. Permanent Residents only with an active DD2345 certification.
The 48th International Conference & Exposition on Advanced Ceramics & Composites (ICACC 2024) will be held from Jan. 28–Feb. 2, 2024, in Daytona Beach, Fla. It is a great honor to chair this conference, which has a strong history of being one of the best international meetings on advanced structural and functional ceramics, composites, and other emerging ceramic materials and technologies.
The Transformative Vertical Flight (TVF) 2024 meeting will take place Feb. 6–8, 2024 in Santa Clara, California, in the heart of Silicon Valley and will feature more than 100 speakers on important progress on vertical takeoff and landing (VTOL) aircraft and technology.
The Program of this Summit consists of a range of 12 high-level lectures by 14 invited speakers only. Topics are composite related innovations in Automotive & Transport, Space & Aerospace, Advanced Materials, and Process Engineering, as well as Challenging Applications in other markets like Architecture, Construction, Sports, Energy, Marine & more.
JEC World in Paris is the only trade show that unites the global composite industry: an indication of the industry’s commitment to an international platform where users can find a full spectrum of processes, new materials, and composite solutions.
Thousands of people visit our Supplier Guide every day to source equipment and materials. Get in front of them with a free company profile.
Initial demonstration in furniture shows properties two to nine times higher than plywood, OOA molding for uniquely shaped components.
The composite tubes white paper explores some of the considerations for specifying composite tubes, such as mechanical properties, maintenance requirements and more.
Foundational research discusses the current carbon fiber recycling landscape in Utah, and evaluates potential strategies and policies that could enhance this sustainable practice in the region.
In its latest white paper, Exel navigates the fire, smoke and toxicity (FST) considerations and complexities that can influence composites design.
New white paper authored by Eike Langkabel, Sebastian de Nardo, and Jens Bockhoff, examines the best resin formulations for composites used in automotive part production, both structural parts and body panels.
Tension control plays a vital role in composites manufacturing in order to achieve automated processing, continuous processing, reduced scrap, increased product quality, and more, says a new white paper released by The Montalvo Corp.
Austrian research institute Wood K plus makes 95% silicon carbide ceramics more sustainable (>85% bio/recycled content), enables 3D shapes via extrusion, injection molding and 3D printing.
Thermoplastic polymer resin was designed to tackle distinctive industry challenges of large-scale 3D printing while also assisting with sustainability initiatives.
The MB9, representing a combination of high performance and eco-conscious materials use, will be commercially available in time for the 2024 sailing season.
For 42 months, the Aitiip Technology Center will coordinate the EU-funded project to design a new range of intermediate materials, such as pellets or resin-impregnated carbon fibers, which will be used to manufacture more sustainable final products.
Co-located R&D and production advance OOA thermosets, thermoplastics, welding, recycling and digital technologies for faster processing and certification of lighter, more sustainable composites.
The German Institutes of Textile and Fiber Research are targeting more sustainable carbon fiber via low-pressure stabilization and bio-based precursors, and working with Saint-Gobain to commercialize oxide ceramic fibers for CMC.
In the Automated Composites Knowledge Center, CGTech brings you vital information about all things automated composites.
CompositesWorld’s CW Tech Days: Infrastructure event offers a series of expert presentations on composite materials, processes and applications that should and will be considered for use in the infrastructure and construction markets.
The composites industry is increasingly recognizing the imperative of sustainability in its operations. As demand for lightweight and durable materials rises across various sectors, such as automotive, aerospace, and construction, there is a growing awareness of the environmental impact associated with traditional composite manufacturing processes.
CW’s editors are tracking the latest trends and developments in tooling, from the basics to new developments. This collection, presented by Composites One, features four recent CW stories that detail a range of tooling technologies, processes and materials.
During CW Tech Days: Thermoplastics for Large Structures, experts explored the materials and processing technologies that are enabling the transition to large-part manufacturing.
Closed mold processes offer many advantages over open molding. This knowledge center details the basics of closed mold methods and the products and tools essential to producing a part correctly.
Explore the cutting-edge composites industry, as experts delve into the materials, tooling, and manufacturing hurdles of meeting the demands of the promising advanced air mobility (AAM) market. Join us at CW Tech Days to unlock the future of efficient composites fabrication operations.
CompositesWorld’s CW Tech Days: Infrastructure event offers a series of expert presentations on composite materials, processes and applications that should and will be considered for use in the infrastructure and construction markets.
Explore the cutting-edge composites industry, as experts delve into the materials, tooling, and manufacturing hurdles of meeting the demands of the promising advanced air mobility (AAM) market. Join us at CW Tech Days to unlock the future of efficient composites fabrication operations.
Thermoplastics for Large Structures, experts explored the materials and processing technologies that are enabling the transition to large-part manufacturing.
MVP's Automated Equipment: Revolutionizing Composites Part Production Through Filament Winding within CompositesWorld's CompositesWorld Collections Knowledge Center
Composites One Offers Manufacturing Efficiencies with Aerovac Kitting Solutions within CompositesWorld's CompositesWorld Collections Knowledge Center
A report on the demand for hydrogen as an energy source and the role composites might play in the transport and storage of hydrogen.
This collection features detail the current state of the industry and recent success stories across aerospace, automotive and rail applications.
This collection details the basics, challenges, and future of thermoplastic composites technology, with particular emphasis on their use for commercial aerospace primary structures.
This collection features recent CW stories that detail a range of tooling technologies, processes and materials.
Transportation issues, rising demands and other factors have led to higher costs or delays for gun rovings and more. Suppliers and Gardner Intelligence share their perspectives.
Fig. 1. Overall business activity of glass fiber manufacturers from 2015 to early 2021, based on data from Gardner Intelligence.
As the coronavirus pandemic enters its second year, and as the global economy slowly re-opens, the worldwide glass fiber supply chain is facing shortage of some products, caused by shipping delays and a fast-evolving demand environment. As a result, some glass fiber formats are in short supply, affecting the fabrication of composite parts and structures for the marine, recreational vehicles and some consumer markets.
As noted in CompositesWorld’s monthly Composites Fabricating Index reports by Gardner Intelligence Chief Economist Michael Guckes, even as production and new orders recover, supply chain challenges continue to persist across the entire composites (and manufacturing in general) market into the new year.
To learn more about reported shortages in the glass fiber supply chain in particular, CW editors checked in with Guckes and spoke to several sources along the glass fiber supply chain, including representatives of several glass fiber suppliers.
Many distributors and fabricators, especially in North America, have reported delays in receiving fiberglass products from suppliers, particularly for multi-end rovings (gun rovings, SMC rovings), chopped strand mat and woven rovings. Further, the product that they are receiving is likely at an increased cost.
According to Stefan Mohr, business director of global fibers for Johns Manville (Denver, Colo., U.S.), this is because a shortage is being experienced throughout the glass fiber supply chain. “All businesses are restarting globally, and we sense that the growth in Asia, especially for automotive and infrastructure projects, is exceptionally strong,” he says.
“At the moment, very few manufacturers in any industry are getting everything they want from suppliers,” notes Gerry Marino, general manager of sales and marketing at Electric Glass Fiber America (part of NEG Group, Shelby, N.C., U.S.).
Reasons for the shortage reportedly include rising demand in many markets and a supply chain that can’t keep up due to issues related to the pandemic, transportation delays and rising costs, and decreased Chinese exports.
Fig. 2. Composite industry activity related to supplier deliveries and production for the glass fiber market. According to Chief Economist Michael Guckes, the height of the supplier deliveries line for early 2021 (shown in green) illustrates the growing proportion of fabricators who are experiencing slow order-to-fulfillment times from upstream suppliers.
In North America, thanks to the pandemic restricting travel and group recreational activities, consumer demand has seen a sharp increase for products such as boats and recreational vehicles, as well as home products like pools and spas. Many of these products are manufactured with gun rovings.
According to Mohr, there has also been increased demand for glass fiber products in the automotive market as automotive manufacturers came back online quickly and sought to refill their stock following the initial pandemic lockdowns during spring 2020. The rebound was apparent, as days of inventory on car lots for some models reached the single-digits, according to data obtained by Guckes.
According to Marino, Q3 and Q4 2020 saw “a much larger surge in demand than we expected,” particularly for chopped glass fiber strands used by customers in the automotive industry, and single-end rovings used in the wind industry.
“All the markets are recovering, some more so than others. In general, our industrial customers have recovered faster and to a greater degree than commercial aerospace, but everything is better,” adds Scott Northrup, VP of sales and marketing at AGY (Aiken, S.C., U.S.).
This growth in glass fiber demand is also strong in China but, reportedly, no substantial capacity has been added to fiberglass production over the past year, meaning that plants are at capacity with no short-term ability to increase production, though demand continues to increase.
Marcio Sandri, president, composites at Owens Corning (Toledo, Ohio, U.S.), adds that the increased demand in recreational vehicle and home improvement products came on top of rapid growth in the wind industry. “All this increased demand took place at a time when industry inventory was already reduced — given intended actions or supply chain issues,” he says.
Figure 2 shows Gardner Intelligence’s supplier delivery and fabricator production data for the glass fiber market. “Never before have we seen the kind of activity spread which currently exists between production and supplier delivery activity readings,” says Guckes. “After recovering to some degree from COVID-19’s initial shock in early 2020, conditions worsened in the fourth quarter. The implication from this is that serious problems still need to be answered; deliveries shouldn’t be this delayed given the modest rebound in production and new orders activity over the last six months.”
One factor, reported by suppliers, is their ability to come back online quickly. Karin Demez, product management lead for global fibers at Johns Manville, says, “We had to adapt to the collapsing demand in Q2 2020 and decreased production of glass fibers on our end. Then we had to make a 180-degree turn and ramp up production again.” According to Marino, much production capacity at NEG and other suppliers had to be idled for much of the second quarter of 2020. “Last summer began a restart period when automotive plants, followed by other markets, began to start up again,” he explains. “It’s been a slow, deliberate process to bring capacity back up.”
In addition, for more than two years, Chinese manufacturers of fiberglass products have reportedly been paying and absorbing most, if not all, of the 25% tariff to export to the U.S. However, as the Chinese economy recovers, domestic demand within China for fiberglass products has increased significantly. This has made the domestic market more valuable to Chinese producers than exporting product to the U.S. In addition, the Chinese yuan has significantly strengthened against the U.S. dollar since May 2020, while at the same time fiberglass manufacturers are experiencing inflation in prices of raw materials, energy, precious metals and transportation. The result, reportedly, is a 20% increase in the U.S. in the price of some glass fiber products from Chinese suppliers.
On top of this, there is a severe imbalance of shipping containers globally, caused by pandemic-induced labor shortages at major sea ports (see Fig. 3). As a result, containers are not emptied in a timely manner, which means empty containers are not available to the shipping supply chain. In some cases, the cost of container freight is reported to have more than doubled since June 2020. Within the U.S., domestic truck shipping has also reportedly risen in price due to lack of capacity and pandemic issues.
Fig. 3. According to a report from Hillebrand, container shipping rates have been surging on all east to west shipping routes since May 2020, and eastbound container freight rates have more than doubled since the beginning of the COVID-19 outbreak.
Transportation issues, of course, affect all markets, within the glass fiber supply chain and otherwise. For AGY, which manufactures in the U.S. and primarily produces glass fiber yarns, the rising costs to ship products to Europe and Asia has been the main issue. “Certain shipping lines have been consolidated, rescheduled or reconfigured, and it’s getting tougher and tougher to get the spaces on vessels to get our materials across the water,” Northrup says.
Sandri adds, “It’s widely known that in the composites industry, price hasn’t kept pace with inflation in many years. The cost of transportation and precious metal used in the production of fibers has increased substantially and there are additional expenses to follow pandemic protocols.”
Fig. 4. This chart tracks six of the business activity measures as provided by glass fiber fabricators. According to Guckes, the February 2021 numbers indicate backlogs are expanding as fast as nearly ever, employment is expanding, supplier deliveries are very slow and exports, production and new orders are outpacing most other manufacturing disciplines.
To return to a more normal supply chain involves many factors, including global vaccination distribution. No one is sure when more normal operations might resume, but estimates CW has heard from suppliers range from the second half of 2021, to the end of Q3, to a year from now.
Owens Corning’s Sandri predicts, “Given the overall shortage of inventory in the industry, increased demand, the required time to ramp up existing idle capacity, and the length of time needed to bring new capacity online, it is likely to be several quarters, possibly even a year, before business returns to normal for the glass fiber reinforcement industry.”
“I’m not sure how transportation issues are going to be alleviated, but especially not in the short-term, the next three to six months,” says Iain Montgomery, director of global business development at AGY. “I think in the longer term normal operations will come back, but I think until then it will be quite tight.”
Johns Manville’s Mohr adds, “We strongly believe that this is only a temporary situation. This is a stress-test for the whole organization as well as for the whole market, but we continue to go every extra mile to keep our customers running.”
Fig. 5. According to Guckes, prices seen by fabricators are rising, but are much lower than actual glass fiber material costs. In many cases, he says, this is caused by small manufacturers preferring to absorb rising material costs rather than pass them along to their customers.
MTorres seeks to enable next-gen aircraft and open new markets for composites with low-cost, high-permeability tapes and versatile, high-speed production lines.
Long glass fiber-reinforced polyamide makes this modular propeller tough enough for a challenging application, eliminating costly prop repair.
Earlier this year I wrote an article on composites recycling and one of the things that struck me was how little fiberglass composite waste was being recycled.
Approaching rollout and first flight, the 787 relies on innovations in composite materials and processes to hit its targets
Quickening expansion in new orders and production activity was counterbalanced by worsening contraction in export activity for the January Composites Index.

Glass Fabric Cloth CompositesWorld is the source for reliable news and information on what’s happening in fiber-reinforced composites manufacturing. Learn More