Disruptive technology with business-critical impact
NOTE: The sponsor of this content may contact you with more information on this topic. Click here to opt out of sharing your email address with this sponsor. (This link will not unsubscribe you from any other BIC email list). 3 Way Gate Valve

Whenever process plant equipment or systems are required to be taken out of service for major maintenance, repair and modification, positive mechanical isolations are provided between the process plant equipment or system and any potential hazardous energy source.
The IK-Group developed and patented AOGV, Add On Gate Valve, Mechanical Isolation Tool is used to install an isolation spade also known as a pipe blind or blanks on a live flanged connection. It can also be used to close or open a spectacle blind or replace a spacer with a line blind while the system is still pressurized. This field proven technology reduces downtime, removes the need for drainage, venting, purging and flushing and it increases your maintenance flexibility.
The AOGV is used to create a zero-energy zone where inspection and maintenance work can be performed safely and efficiently, plus it leaves no lasting impact to the process plant. Once the operation is complete, the flange pair is returned to its original pipe spec state with a new gasket, bolts, and nuts.
The AOGV is versatile – typical AOGV applications include:
HOW DOES THE AOGV WORK?
The AOGV technology is basically a gate valve that can be assembled in pieces over any live flange pair upstream or downstream of the pipework or equipment requiring intervention. The AOGV isolates on the flange circumference and once the flange pressure is contained within the AOGV housing, the flanges are separated, cleaned and either an isolation spade inserted for isolation purposes or a gasket may be removed and replaced.
The AOGV parts are assembled over the live flange pair whilst the pipe medium is left in place.
Flanges are separated, the gasket removed and the blind spade is inserted.
The required intervention or work is performed and the blind spade is retracted.
A new gasket is inserted, bolts torqued, and the system returned to its original specifications.
Positive Isolation is regarded as the most secure method for energy isolation and the use of the AOGV can facilitate for either:
The AOGV has been approved by and is in use by several of the oil and gas supermajors and multinational NOCs on both upstream, downstream, and integrated gas assets. The tools meets all relevant standards – EN 13445, ASME PCC2/B31.3, PED2014/68/EU and are CE marked by DNV.
Passing valves and leaking flanges is a challenge for any process plant and the AOGV can facilitate valve and seal replacements and repairs as and when needed, without having to wait for or trigger a full or partial facility shutdown. In addition, by reducing the isolated area more of the process inventory is left in the plant, thereby reducing the risk for spill and volume of emissions.
As for all assets the execution of site activities should be done so that facility downtime is kept to a minimum, asset integrity is maintained, and the risk is mitigated to “as low as reasonably practicable”. Built-in isolation points can require partial facility shutdowns and the ejection and flushing of large inventory volumes. Work scopes can come at a significant production loss and personnel are more exposed to risk the more extensive the activity. By using the AOGV to bring the isolation point closer to the point of interest, the area impacted by the work is reduced and subsequently the likelihood of a shutdown and large ejection of inventory.
By having the ability to insert an isolation spade at any live flange pair, the AOGV can isolate individual pieces of equipment where no other means are provided and make it possible to execute work outside of a turnaround or without having to shut down the process plant, therefore increasing asset uptime.
The AOGV technology offers value by reducing the time spent “in-plant” and area of the facility impacted. Compared to alternatives, the AOGV allows for:
“For what temperature and pressure can the AOGV be used?”
The temperature range is from - 280°F to + 400°F (-173°C to +200°C)
Pressures up to 2500 psi (175 bar).
“For what sizes of pipes and pressure class combinations can the AOGV be used?”
We have been focusing on the ASME class 150 & 300 in sizes from 1” to 24” but have tools that can handle sizes up to 36” ASME and up to class 2500. Please see our tool fleet at AOGV.com for available, off the shelf sizes and class combinations.
“How much clearance does the AOGV need either side of the flange to be installed?”
As a rule of thumb, for pipes from 1”to 4” the AOGV needs 2” of clearance and from 5” and upwards a 1/2 pipe diameter is needed. This is measured from the bolts and nut side of the flange.
“How is the AOGV going to seal on the full circumference of the flange and the bolt holes?”
The seal is pre-energized, acts as a plug, and seals directly from the circumference surface all the way to the inside of the AOGV. The bolt holes are also plugged with mechanical plugs bolted to the AOGV kit. The seal is typically an elastomer to make sure uneven surfaces can be sealed properly.
“Can the AOGV be fitted on the flange of a 3-piece valve?”
The AOGV can be fitted on most valve types and nozzles including 3piece valves.
“Does the pipe have to handle the weight of the AOGV?”
For some of the smaller sized AOGV’s the pipe can easily handle the weight but common practice is it to suspend the weight of the AOGV in chain hoists attached to a superstructure or scaffolding above the AOGV.
“What about the condition of my flange?”
When the team set up the AOGV, we remove your old gasket at the beginning of the operation and replace it with a new gasket at the end. So far, every operation has been successfully executed with a new gasket installed and system successfully recommissioned.sealed
“How do you perform the splitting of the flanges after the AOGV has been installed?”
Either the system pressure is used for splitting the flanges or the pipe is gently moved physically e.g. with chain hoists to pull them apart. The stress tolerances are calculated for the displacements, and we analyze where in the plant you’re able to give a little with your pipe to handle the movement. The movement itself is carefully controlled and monitored by gradually releasing the compression exerted from the integrity clamps.
For more information, please contact AOGV Business Development Manager - Kenneth Låtveit (kenneth.laatveit@ik-worldwide.com) or visit AOGV.com
Connecting people in business and industry with one another for the betterment of all. Become a BIC Alliance Member today.
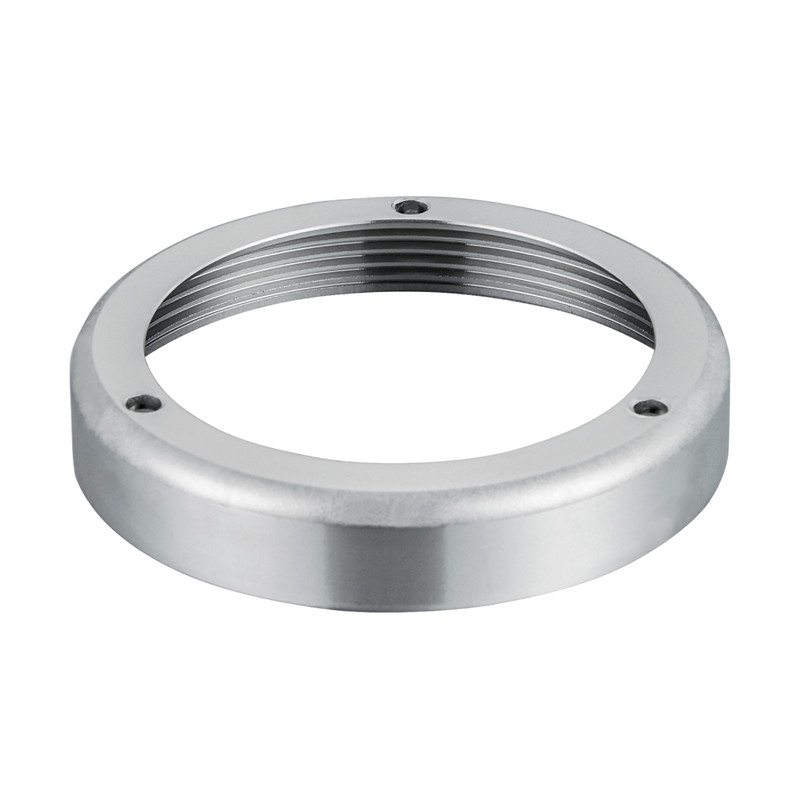
Residential Water Meter Copyright © 2024 BIC Alliance, Inc. All rights reserved.