The whirring of machines stops for an hour in the afternoon. Before heading for their lunch break, V. Kumaran, a worker, checks the PH levels at the biomethanation plants at the Sri Velmurugan Sago factory in Tamil Nadu’s Salem district.
The biomethanation process in these plants is when the wastewater produced in the sago manufacturing process, is used to convert organic waste to biogas. The biogas generated, in turn, is used to generate electricity which has been a game-changing move that reduces the factory’s power costs. Sweet Potato Starch Machinery
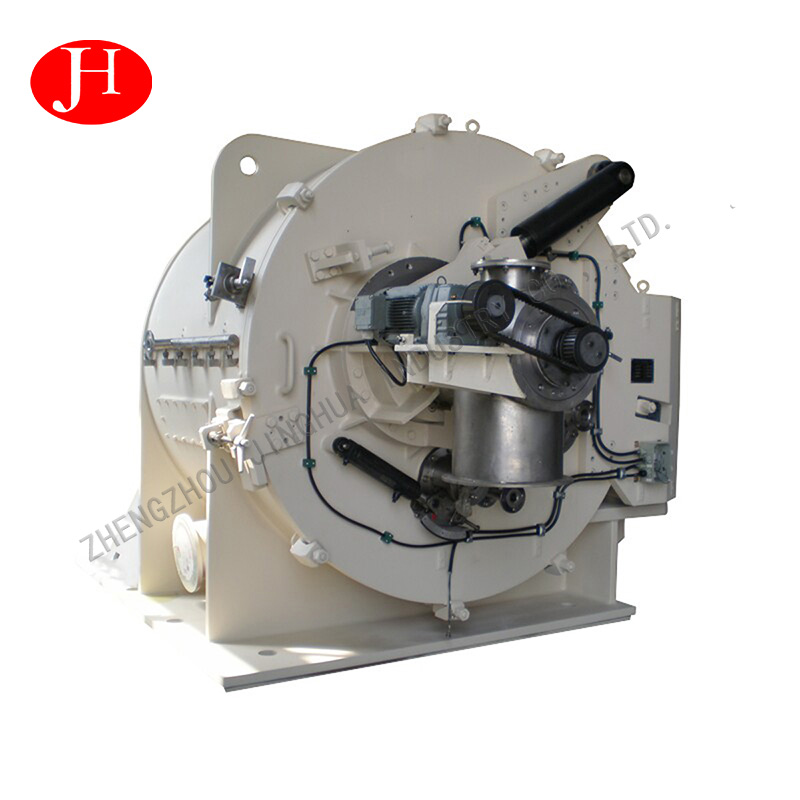
Sri Velumurugan Sago factory, located in the state’s Attur taluka in Salem district, runs for 20-22 hours a day, consuming 125 units of electricity per hour. From cleaning the tapioca (raw material used to manufacture sago) to crushing it and sedimenting the tapioca powder, every step of sago production is water and power intensive.
The tropical, humid climate in Salem district favors tapioca cultivation (locally called kuchi kizhangu). Tapioca is processed into starch, which is used as a binding ingredient in medicinal tablets and to add concentration in the food and beverage industry. Starch is later processed into sago, which has a huge market in Maharashtra and Assam.
Source: Ministry of Small and Medium Enterprises (MSME)
Sri Velumurugan Sago factory operates for 22 hours a day, consuming 2,750 units of electricity a day and 82,500 units a month. “If not for the biogas, I would be paying Rs 6.18 lakh (Rs. 618,999) – calculated as 82,500 X 7.5 which is the Tamil Nadu Electricity Board’s commercial tariff rate – a month. But I pay less than a lakh (Rs. 100,000) only to compensate for the days when biogas is not generated and pipelines are under maintenance,” said founder, V. Krishnan.
While the low tariff benefits are there, the capital cost of setting up a biomethanation plant is high. And while government schemes promise, on paper, subsidies for biogas generation, accessing these subsidies is a challenge for the beneficiaries.
Krishnan spent around Rs. 70 lakhs (Rs. seven million) to set up three plants that treat 3.5 lakh (350,000) litres of wastewater every day. “I set up a biogas plant in the year 2000 and two more plants in 2010. If I were to set up these plants now, it would cost me more than Rs. two crores (Rs. 20 million). I tried to get the subsidy from Tamil Nadu Energy Development Agency (TEDA) and Khadi and Village Industries Commission (KVIC), but in vain,” said Krishnan, who relied on bank loans to set up the existing plants.
“The reasons (for not getting subsidy) are irrational. The Khadi Commission wanted us to set up floating drum biogas plants to avail the subsidy. That incurs so much more investment that the subsidy wouldn’t be of any use,” Krishnan said. He couldn’t avail the subsidy from TEDA as the department was not convinced with the design of the biomethanation plant. “None of the departments guided us with the design and technology for setting up these plants. We did the research and got inputs from experts to set them up ourselves,” said Krishnan.
“The subsidy from the Khadi Commission was active only for a year (in 2010). When I applied for it, I was told that it is no longer implemented,” said Arun (who prefers to share only his first name), Proprietor, Golden Sago Factory in Tamil Nadu.
At COP26, India announced its ambition to become a net-zero emitter by 2070. As a country that produces close to 500 million tonnes of agricultural waste per year, there is a huge potential for producing biogas in India, writes energy analyst Samiksha Shrivastava, in a 2022 article for the ICF, a global advisory and technology services provider.
While Salem’s sago industry is a pioneer in biogas production from wastewater in India, a push from the government can increase the production multi-fold because not every factory owner can afford to install biomethanation plants. So, sago factory owners install plants that treat only part of the wastewater.
A sago factory located at Attur has a biogas plant that treats two lakh (200,000) litres of wastewater every day, while the total wastewater discharge in the factory per day is around 0.4 million litres.
“I spent a crore (Rs. 10 million) to install this plant for which I am still paying debts. TNPCB officials are now threatening us to shut our factory if we don’t set up another plant to treat the 0.2 million litres of water, but none of the government departments including TEDA, KVIC and the Ministry of Food Processing Industries are issuing a subsidy for the new biogas plant,” said the factory’s proprietor, who preferred to remain anonymous. The factory proprietor expels the untreated two lakh (200,000) litres of wastewater onto his farm every day, defying the norms of TNPCB.
“Factories use various strategies to dispose their wastewater without treatment. Few factories dig up borewells to 500 feet to dispose the water inside these wells. They are aware that the groundwater is found only at 1000 feet,” MSME Minister T. M. Anbarasan told Mongabay India.
For many sago factory owners, setting up biogas plants is just a task to comply with the pollution control board. Few factories set up biogas plants only after their factories were shut down by TNPCB. Some others installed biogas plants only after receiving closure orders from the TNPCB.
In the past five years, a total of 23 sago industries have been issued with direction for closure and stoppage of power supply, according to the TNPCB’s Salem district engineer, Senthil Vinayagam. “TNPCB issued closure orders as the capacity of biogas plants in these factories are much less than the wastewater produced every day. While less than 10 of them reopened after increasing the plant capacities, others remain shut,” said Vinayagam.
For the sago industry, TNPCB mandates aerobic (with oxygen) treatment of wastewater followed by anaerobic treatment (without oxygen) to keep the Biochemical Oxygen Demand (BOD) standard of the land in check (100mg/ litre). Only one out of 12 factories, that Mongabay India interacted with, had this set up. The rest only do anaerobic digestion of waste through a biomethanation method.
But unlike biomethanation, the operating cost of aeration is high. “My factory produces 4.5 lakh (450,000) litres of wastewater every day. To treat it through aeration, I spend Rs 1.5 lakh (Rs. 150,000) a month. It doesn’t give me any profits, but I am glad that the soil is conserved completely,” said Bharath M., manufacturing member, Salem Starch and Sago Manufacturers’ Service Industrial Co-operative Society Ltd (SAGOSERVE). Bharath’s factory is the only factory that follows the TNPCB mandate among 12 others Mongabay India spoke to.
“Installing a biomethanation plant of one lakh (100,000) litres capacity costs Rs. one crore (Rs. 10 million). Around 2500 cubic metre of gas can be generated through a lakh (100,000) litres of wastewater. To store the gas, a 250 Kva generator that costs Rs. 40 lakhs (Rs. four million) is required,” said Balaji Armugam, biomethanation consultant to many sago factories. So, gas produced in one lakh (100,000) litres of wastewater can keep a generator of 250Kva running for 10-12 hours.
The high number of suspended solid contents and insoluble fibres present in the byproducts of sago production are a cause of serious environmental pollution if let out without treatment. “Every kilogram of water contains 5 gm of volatile solids. These solids are converted to liquids through solid-liquid bacteria and then to gasses by feeding in the bacteria in the biomethanation plant,” explained Armugam, adding that the procedure takes 30-45 days.
Without sufficient support from the government, sago industry owners find it hard to invest the money. “By opting for bio-gas, we are also reducing the burden on thermal power. Subsidies from the government would only encourage us to set up more plants,” said Arun.
In 2022, TNPCB received no proposals from factories to set up new biogas plants.
Nine out of 12 factory owners that Mongabay India interviewed in Salem and its neighbouring districts confess that they have smaller capacity biogas plants than they require as per the TNPCB guidelines. All of them attributed it to the lack of subsidies to setup biogas plants.
Based on the anecdotes from factory owners, the subsidy for biogas plants from the Khadi Commission and MNRE were available only for a brief period. While subsidies from Khadi Commission were hard to access due to non-compliance of design, factory owners are not even aware of the subsidies released by MNRE.
MNRE officials, however, paint a different picture. “The National Bioenergy Programme provides ample opportunities for developers working in waste to energy space. Even before this, MNRE offered many subsidies to TEDA under the waste to energy programme,” said Dinesh Dayanand Jagdale, Joint Secretary, MNRE. The Joint Secretary couldn’t provide information related to the specifics (such as name and year of implementation) of the programme or the data related to the beneficiaries. TEDA officials did not respond to Mongabay India’s queries on data about subsidy beneficiaries.
“Between 1997 and 2000, subsidies were provided for the sago industry for biogas generation projects,” said Arun K. Tripathi, Scientist G, MNRE.
In 2021, MNRE unveiled the National Bioenergy Programme through which the Central Financial Assistance (CFA) would be provided for projects for setting up large biogas plants for the period of 2021-22 to 2025-26. “The scheme supports not just the new biogas plants but also the old and existing ones. In the case of sago industries, as developers are generating biogas from the existing infrastructure, CFA will be provided for conversion of biogas to BioCNG (@Rs 3.0 Cr per 4800 kg/day) or biogas to power (Rs 0.5 Cr /MW),” said Ganesan Natarajan, a biogas expert and Chairman of Topaz Solar Private Limited.
However, sago factories owners complain they were not made aware of the financial assistance from the central government. “Neither MNRE nor TEDA took efforts to sensitive the small scale industrialists about the scheme. Does this scheme include the sago industry? How do we benefit from it? We do not know where to seek out answers to these questions,” Krishnan said.
“It is only fair for the government to subsidise biogas plants now to compensate for years of step motherly treatment,” said R. M. Vijayamoorthy, proprietor of Golden Sago Factory in Salem district.
According to a 2002 research paper in the Indian Journal of Environmental Protection, on the treatment of sago factory effluents, the environmental hazards of untreated water have long been understood. “The release of high content of the organic load along with the effluent when stored, results in obnoxious odour, irritating colour, lower pH and higher Biochemical Oxygen Demand (BOD) and Chemical Oxygen Demand (COD) (Ayyasamy et al. 2002). When the effluent is released into the environment without proper treatment, it alters the characteristics of the ecosystem. Farmers, using these raw effluents for irrigation, found that the growth [of crops], yield and soil health have reduced,” the paper’s authors state. BOD is the amount of oxygen required by microorganisms to decompose the organic matter. Higher BOD levels makes it difficult for organisms to feed on the water and if the organisms don’t feed on the water, its quality remain poor.
The hazards of untreated wastewater on soil and water is alarming, say experts. “For decades, sago industries let untreated water into agricultural land, due to which fertility has been affected. The expanding capacity of the starch blocks the soil pores and hinders air from penetration. This has affected the characteristics of soil, making it unlivable for microorganisms,” said a TNPCB official who worked at Salem for five years. He requested to be anonymous.
The degradation of water is evident from the changes in crop patterns. “Crops such as paddy and sugarcane that require ample amounts of groundwater are now substituted by cotton and coconut plantations,” mentioned a research paper submitted to the Indian Journal of Economics and Development. The study was conducted in 2017 in the villages close to the sago factories in the Salem district.
Due to high starch content, biogas production is deemed to be one of the ways of wastewater management in dairy, beer, sugar and pulp manufacturing industries.
“Only 1 out of 20 sugar mills have set up biomethanation plants. Press mud, a compressed sugar industry waste, with high COD values, is disposed of in abandoned spaces and water bodies while in their reports to the government, they say that the waste is used for composting. For every 2000 tonnes of sugarcane, 100 tonnes of press mud is generated,” said Parthasarathy, a biogas expert, who has set up biomethanation plants for food and beverage industries in South India.
Under the waste to energy scheme, MNRE provides a central financial assistance of Rs. one crore (Rs. 10 million) per 12000 cubic metre of biogas generation per day and Rs. four crores (Rs. 40 million) per 4800 kg/day for Bio-CNG generation. Providing subsidies encourages factories’ management in installing an adequate number of biogas plants, generating energy from non-fossil fuel sources and in addition, curbing environmental pollution.
This story was produced with the support of Internews’ Earth Journalism Network.
Banner image: Biogas fumes generated from waste water produced after treatment of sago. Photo by Laasya Shekhar/Mongabay.
Mongabay improves understanding of the concurrent global scale forces undermining the health of Earth’s systems. Mongabay makes science accessible and elevates the voices and knowledge of people directly impacted by environmental change.
Mongabay-India is a conservation and environment news and features service that aims to bring high quality, original reports from nature’s frontline in India.
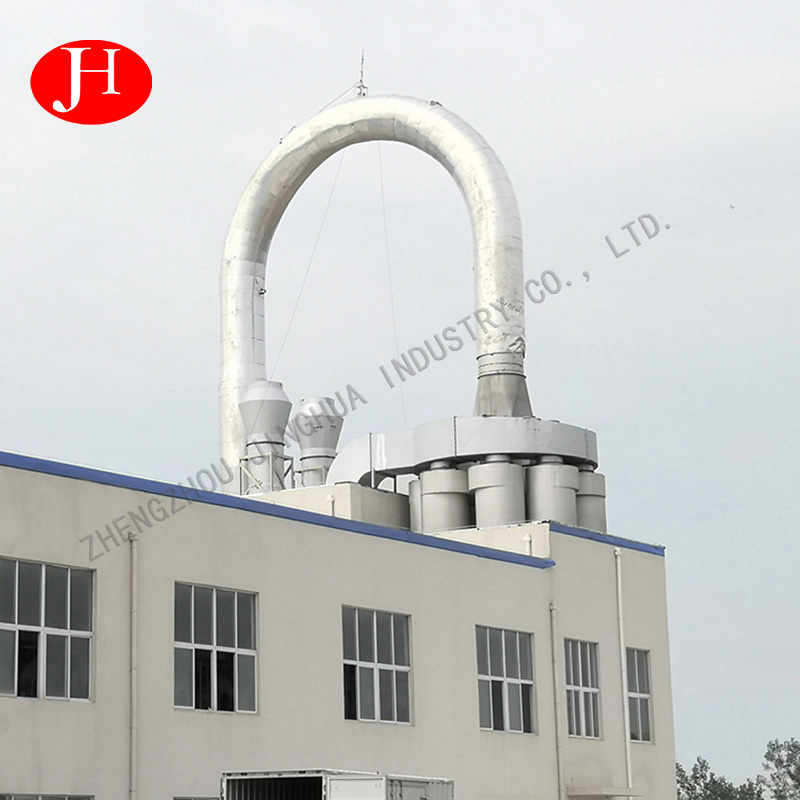
Starch Vacuum Filter Machine Get fact-checked science and environment news from India in your inbox every Saturday!